Thermospray
Project description:
H.C. Starck Tantalum and Niobium GmbH have developed a new technology for the hydrometallurgical production of niobium oxides, a so-called "thermal decomposition of niobium-containing solution". This process is being further developed and transferred to the technical scale. The main features are significantly reduced production costs and a minimal environmental impact through sustainable recycling of process chemicals. So far, the new technology of thermal spray decomposition has been investigated on a pilot scale.
In the next step, a scale-up has to be carried out to investigate the long-term material and process stability as well as the reproducible product quality. In summary, the most important tasks in the next project steps are
- Upscaling, reconstruction and retrofitting of the experimental plant for the demonstration phase
- Investigation of the long-term resistance of the materials used in the production plant to corrosion
- Overview of the reproducibility of the process in terms of product quality
- Adaptation of the product quality by mechanical processing
The main advantages of the new technology are
- significantly reduced production costs
- Development of new product qualities
- significant reduction of waste water and sludge production
- Sustainable recycling of process chemicals
Niobium oxide from thermal spray decomposition technology can be used as a precursor in various applications. Target applications for niobium oxide obtained by thermal spray decomposition are Nickel-niobium alloys, lead-free piezoceramics and others, e.g. optical industry.
The "ThermoSpray" project consortium consists of three partners (HC Starck Tantalum and Niobium GmbH, Clausthal University of Technology and AGH University of Science and Technology), which are from the fields of business, industry, education and research. Partners from CLC East and CLC West will be brought together.
Network partners:
- H.C. Starck Tantalum and Niobium GmbH
- TU Clausthal
- AGH University of Science an Technology
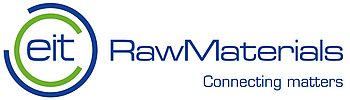
EIT RawMaterials
Project number: 18328